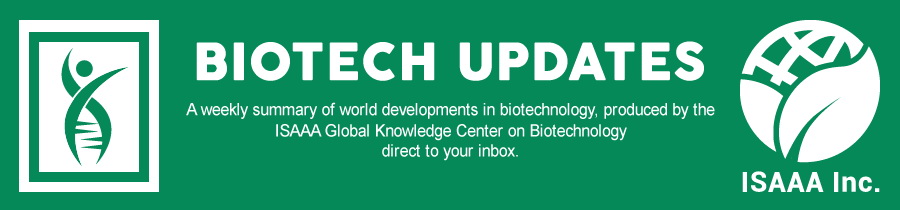
Techno-Economic Impacts of Pretreatment Options in Cellulose-Ethanol Production from Model Grass Analyzed
September 23, 2011http://www.biotechnologyforbiofuels.com/content/4/1/27/abstract
|
The production of ethanol from lignocellulosic biomass usually involves three sequential processes: (1) pretreatment, for lignin removal and liberation of complex carbohydrates in the biomass, (2) saccharification, for the conversion of the liberated complex carbohydrates into simple sugars, and (3) fermentation of simple sugars to ethanol. The pretreatment step offers the most number of technological options. Common pretreatment methods include the use of dilute acid, dilute alkali, hot water (hydrothermal treatment) or steam explosion treatment.
Cost-effectiveness is the primary consideration for the selection of a good pretreatment method, but techno-economic comparisons among different pretreatment options have been difficult. This difficulty has been attributed to the fact that process models have been developed only for individual pretreatment process, without looking at the "overall picture" of the cellulose-ethanol production process. A "lack of a consistent process modeling framework for the underlying ethanol production process" reportedly makes comparison difficult.
Researchers from Oregon State University (United States) attempted to develop process models for four common pretreatment processes under a "consistent underlying framework", in order to investigate "economic feasibility, compare energy consumption and sensitivity of the ethanol price to process parameters". Using a grass-based, tall fescue (Festuca arundinacea Schreb) straw as the model feedstock, they compared the techno-economic factors for the following pretreatment methods: dilute acid, dilute alkali, hydrothermal and steam explosion.
Among the highlights of the study are: (1) hot water (hydrothermal) pretreatment had the lowest unit ethanol production cost, due to non-use of chemicals while achieving comparably reasonable pretreatment efficiencies, (2) the capital cost of an ethanol production plant was lowest for steam explosion, due to a "high solids loading assumption" during pretreatment and hydrolysis, (3) ethanol production cost was shown to be sensitive to pentose fermentation efficiency, (4) energy from lignin residue was found to be sufficient to supply total steam requirement for the production plant (for all pretreatment options), (5) water use in the production process using steam explosion, (6) potentials for reducing ethanol production cost are in increasing pentose fermentation efficiency and reducing the costs of biomass (feedstock) and enzyme. The full article is published in the open-access journal, Biotechnology for Biofuels.
|
Biotech Updates is a weekly newsletter of ISAAA, a not-for-profit organization. It is distributed for free to over 22,000 subscribers worldwide to inform them about the key developments in biosciences, especially in biotechnology. Your support will help us in our mission to feed the world with knowledge. You can help by donating as little as $10.
-
See more articles:
-
News from Around the World
- The Benefits of Biotech to Agriculture
- Benefits of Good Nutrition Take Center Stage at UN High-Level Event
- Science Communication to Step Up in Muslim Countries
- US Embassy in Gambia Conducts Biotech Seminar for Policy Makers
- Scientists Develop New Potato Lines to Wage War on Wireworms
- Breeding Soybeans for Improved Feed
- Scab Resistance in Durum Wheat
- Crop Genetics to Battle Harsh Conditions
- Texas Center Aims for Drought Tolerant Melons
- Hidden Link in DNA of Plant
- Variety Market Development: A Bt Cotton Cropping Factor and Constraint in China
- Notice of License Application for Limited and Controlled Release of GM Wheat and Barley
- Indonesian Farmers Learn Biotech Crop Adoption in the Philippines
- York Scientist to Produce Biofuel from Orange Peel
- Adoption of GM Crops in Spain Reaches Record High
- Butterflies on Bt Corn Not at Risk in Nature
- DEFRA Approves Wheat Trial
- Swiss Consumers: Freedom of Choice and GM
-
Research Highlights
- Scientists Develop Blight-resistant Potato using Ensifer-mediated Transformation
- Researchers Investigate Molecular Mechanisms of Duplicated Genes in Tobacco
- Improved Phosphate Uptake in Alfalfa Seeds by Overexpression of Genes from Medicago truncatula
-
Beyond Crop Biotech
- Blind Circadian Clock of Cavefish Enlightens Scientists
- Online Gamers Help UW Researchers Solve AIDS Mystery
- 'Gloomy' Gene May Make People More Positive
-
Resources
- Feeds: Genetically Modified
- Philippine Agribiotechnology Annual Report
-
Read the latest: - Biotech Updates (June 25, 2025)
- Gene Editing Supplement (June 25, 2025)
- Gene Drive Supplement (February 22, 2023)
-
Subscribe to BU: - Share
- Tweet