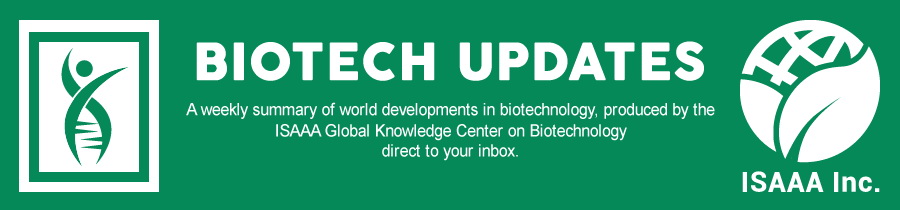
Novel Enzyme-catalyzed Process for Continuous Commercial Scale Biodiesel Production
August 12, 2011(complete access to journal article may require payment or subscription)
http://pubs.rsc.org/en/Content/ArticleLanding/2011/EE/c1ee01295a
http://www.thebioenergysite.com/articles/982/enzymatic-catalyst-for-biodiesel-production
http://www.physorg.com/news/2011-07-enzymatic-catalyst-biodiesel-production.html
|
In biodiesel production, plant oils are usually reacted with an alcohol (commonly,methanol) to produce a mixture of compounds known as methyl esters (the "biodiesel" product). The reaction (which is called "transesterification") is usually catalyzed by a base, such as sodium hydroxide. Because base-catalysts can reduce the biodiesel yield due to side-reactions, scientists are exploring alternative catalyst-materials.
Alternative catalysts for the transesterification reaction in biofuel production are enzymes, such as those that belong to the family of lipases (triglyceride hydrolases). Lipases are said to be efficient and selective for the transesterification reaction. However, the cost and possible instability make enzymes unfavorable for industrial biodiesel production applications.
A team of French researchers from French National Center for Scientific Research (CNRS), the Institute for Molecular Sciences (France) and the Laboratory of Condensed Matter Chemistry (France) report a way to overcome the above-mentioned problems. They employed monolithic biohybrid foams to confine the enzymes for a relatively long period of time (approximately 2 months). Confinement in the biohybrid foams allowed good accessibility and enhanced mass transport, resulting in a high biodiesel yield. The long term stability of the enzymes make the process attractive for commercial applications. The researchers then devised a method for the in-situ production of the new biocatalyst in the reactor itself; thus, allowing uninterrupted, continuous, unidirectional flow industrial production of this biofuel. The biodiesel yields from this novel method were the best achieved so far and it met all the current energy and environmental requirements and standards. According to the researchers, the next step in the research is the solvent-free conversion of triesters, aimed at minimizing waste production by curbing the use of solvent sand metals in chemical transformation processes. The full study is published in the journal, Energy and Environmental Science (URL above).
|
Biotech Updates is a weekly newsletter of ISAAA, a not-for-profit organization. It is distributed for free to over 22,000 subscribers worldwide to inform them about the key developments in biosciences, especially in biotechnology. Your support will help us in our mission to feed the world with knowledge. You can help by donating as little as $10.
-
See more articles:
-
News from Around the World
- First Systematic Network Map for Arabidopsis
- Antigua and Barbuda: 26th Signatory to the Cartagena Protocol on Biosafety
- Ethiopia Releases Wheat Varieties
- FAO Calls for Action to Arrest Famine in Africa
- Egyptian Agriculture Minister Acknowledges Role of Biotechnology
- Batelle Study: Agriculture and Agbioscience Crucial for Economic Growth
- USDA Scientists Use New Technology to Detect Citrus Greening
- Research on Wheat in Canada
- USDA and DOE Fund 10 Projects to Accelerate Bioenergy Crop Production
- Book Chapters on Communication Challenges in Crop Biotech Available Online
- ISAAA Releases Two New Publications on Impact of Bt Cotton in India
- Building Urban-Rural Alliances to Respond to Food Security Issues
- Think Global, Act Asia to Address Food Security
- Jones: Private Companies Should Partner with the Public Sector in Developing GM Crops
- Simple Database to Select Promoters for Plant Transgenesis
- JHI Researchers Discuss What's Next for Potato
-
Research Highlights
- A Novel Rice Spotted-leaf Gene Found in Rice
- Effects of Hydrolysis on Structure and Antioxidant Activity of a Barley Protein
- Field-Evolved Resistance to Bt Maize by Western Corn Rootworm
-
Beyond Crop Biotech
- Approval Uncertainty for GM Salmon Affects Food Production Efforts
- Frankia Produces Natural Products
- Why Small Squids Have Big Sperm
- Stomach Cancer Tumors Have Genetic Differences: Researchers
-
Announcements
- Food and Nutrition in the 21st Century, Warsaw, Poland
- Plant Genome Evolution Conference
- Vavilov-Frankel Fellowship Call for 2012
-
Resources
- Genetically Modified Food and Global Welfare
-
Read the latest: - Biotech Updates (July 9, 2025)
- Gene Editing Supplement (June 25, 2025)
- Gene Drive Supplement (February 22, 2023)
-
Subscribe to BU: - Share
- Tweet